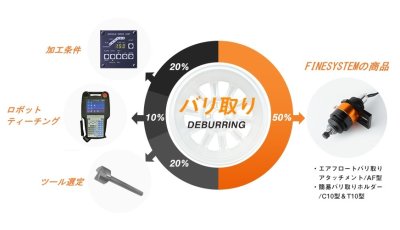
2024.03.01
「バリ取り自動化」に革命を|FINESYSTEMのバリ取りシステム開発について
製造業界において、バリ取りは長年にわたり重要かつ煩雑なプロセスとして存在してきました。バリとは金属やプラスチックなどの加工過程で生じる「余分な部分」のことで、これを除去することが製品の品質や機能性に直結しています。 従来、この作業は熟練の作業者による手作業が中心であり、時間がかかる上、精度の面でもばらつきが生じがちでした。そこでFINESYSTEMでは、このバリ取りを機械やロボットを用いて自動化させることで、モノづくりの精度・生産性をより向上させるため、日夜研究を続けています。 本記事では、FINESYSTEMが手がける「バリ取り自動化」の特徴や、精度・品質向上に対する研究の裏側について、詳しく解説していきます。 「バリ取り自動化」の重要性と課題 これまで主流であった「手作業によるバリ取り」というのは、高精度で確実な除去ができる反面、時間がかかる上に、作業者に大きな負担をかけるという課題がありました。さらに、作業者の「熟練度」や「疲労状態」によって、品質にバラツキが生じてしまうことも、大きな課題とされています。 そこで近年では、機械(ロボット)を導入し、作業効率の向上・品質の向上(バラツキ低減)を行う企業が増えてきているのです。 一方で、機械を導入するにあたっても、さまざまな課題が残っているのもまた事実です。例えば設備導入後についていえば、運用方法を理解し、適切にメンテナンスできる技術者が必要ですし、新製品追加や機種変更された場合には、その都度、設備の改造や交換ができる人材が必要になります。 また複雑な形状や、特殊な材料を扱う場合は、機械では精度が不充分で、結局一部を人の手でバリ取りしたり、より精度の高いロボットを買い直したりしなければならないなどのコスト面・時間的な面でのデメリットが多くあったのです。 FINESYSTEMの解決策 FINESYSTEMでは日本のモノづくりを支えるべく、バリ取り自動化における課題解決に日夜取り組んでいます。そこで私たちが辿りついた答えが「FINESYSTEM独自のバリ取り理論」です。 当社はオリジナルのバリ取り理論に則り、バリ取り熟練工の技をバリ取りロボットセルに置き換えるというコンセプトのもとバリ取りの自動化をご提案しております。 オリジナルのバリ取り理論とは、バリ取り作業を100%とした場合、そのうちの50%が当社のエアフロート式バリ取りアタッチメントや簡易バリ取りホルダ、20%がツールの選定、20%が加工条件、10%がロボットティーチングという考え方です。ここからは、当社のバリ取り理論に沿った、バリ取りシステム開発の裏側をご紹介します。 1:生産から導入後のサポートまで、グループ5社による完全連携 FINESYSTEMを含む「ファイングループ」では、5社(FINESYSTEM・ROBOSYSTEM・司工機・ファインテクノ・FINEPLUS)が連携することで、バリ取り自動化の「自己完結型一気通貫生産システム」を構築しています。 従来のロボット開発というのは、開発は開発会社、導入・システム管理はそれらに特化した会社と分割されることが一般的でしたので、トラブル対応への遅れや機械への対応人材の不足などが、設備導入の足かせとなることが多くありました。 そこで我々は、グループ会社として作業をすべて内製化することで、バリ取りシステムの開発・導入から、保守・トラブルサポートまで、迅速な対応を実現しています。一日の遅れも許されない製造業界だからこそ、徹底した管理体制に支持をいただいています。 2:バリ取り精度を高める「エアフロート式バリ取りアタッチメントAF型」の導入 いくらバリ取りが効率化されても、バリ取り品質が落ちては意味がありません。近年では、刃先が「X・Y・Z」方向に傾動または伸縮することで、バリ取りの精度をより高められる「フローティング機構」を取り入れたバリ取り工具が主流となっています。 一般的なフローティング機構というのは、バネ(スプリング)の力で伸縮するものが主流となっていますが、当社の開発する「エアフロート式」は、バネ式同様に刃先が「X・Y・Z」方向に傾動・伸縮するのに加え、フロート力は圧縮エアによりピストンを押すことで発生します。 これによりフロート力を「エア圧の調整」だけで簡単に行えるため、箇所ごとのバネ交換が不要となります。またフロート力(圧力)がバネの縮みに比例するスプリング式とは異なり、エアフロート式ではほぼ一定のフロート力が得られるため、まるで熟練工の手作業のような動きの自動化を実現しました。 当社が開発する「エアフロートシステム」については、下記記事もあわせてご覧ください。 関連記事:『フローティング機構とは|バリ取り自動化に向けて知っておきたいこと』 3:ツール選定・加工条件・ロボットティーチングまで徹底管理 実はバリ取りを効率化するためには、ロボットを導入するだけでは不充分です。例として、当社がツール選定や加工条件、ティーチング(プログラミング)を最適化することによりバリ取り品質を改善し加工時間を短縮できた事例がございます。 当社のエアフロート式バリ取りアタッチメントで他社がバリ取りを自動化したお客様より、目標のバリ取り品質や加工時間を達成できないとご相談をいただきました。当社の作業者がお客様の自動バリ取り機のツール選定、加工条件、ロボットティーチングを修正しました。 このように当社のエアフロート式バリ取りアタッチメントと最適なバリ取り条件を提供することにより、加工時間を約30%短縮しながらバリ取り品質についてもお客様より合格の判断をいただくことができました。 いわゆるバリ取り機を導入すれば、ある程度の効率化や品質向上は可能ですが、使用するツールやティーチングまでこだわらなければ「高品質で効率的なバリ取り」は実現できません。当社ではロボット導入から始まり、ツール選定や加工条件、ティーチング作業までをすべて一貫して提供しております。これが「FINESYSTEM独自のバリ取り理論」の答えなのです。 当社のバリ取りシステムによる素材別事例 <鉄の加工事例> <アルミの加工事例> FINESYSTEMなら、バリ取り自動化における 導入からティーチングまで一括サポート! これまでバリ取りをロボットで自動化するためには、機械設置やロボットティーチング(プログラミング)などの専門的な知識のある人材が必要とされてきました。 そのため、バリ取り自動化を前向きに検討されている企業の中でも、 自社でできるかわからない… 導入後のプログラミング(ティーチング)ができる技術者がいない… ロボットに熟練工レベルの仕上がりが再現できるのか不安… などのお悩みから、導入を諦めてしまう企業様も少なくありません。 FINESYSTEMでは、ロボットを活用したバリ取りに関するあらゆる自動化で、お客様のお悩みを解決し生産性向上のお手伝いをします!「無償バリ取りトライ」も行っており、事前にバリ取り品質をご確認いただけます。 上記のような内容でお悩みなら、ぜひ一度お問合せくださいませ! >>お問い合わせはこちらから >>バリ取り・RBハンドリングのトライのご相談はこちらから