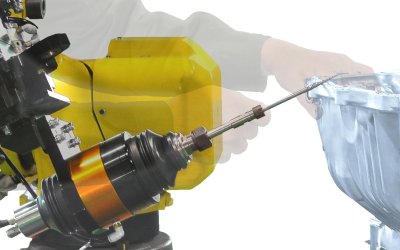
2024.11.13
真の“バリ取り自動化”とは何か?「空振り・えぐりゼロ」を実現するバリ取り機の開発背景
FA化(工場自動化)が進む今日、製造業におけるバリ取りもロボットによって自動化する企業が増えつつあります。バリ取り機製造を行う多くの企業が「バリ取り自動化」を謳っていますが、実際のところどうでしょうか。 最終的な仕上げは「人の手」で行われている 複雑なワーク形状の場合、まだまだ手作業に頼らざるを得ない これを「“自動化”と呼んでいいのか…」。我々はこの業界課題に疑問を投げかけ、バリ取りの完全自動化に真正面から取り組むことを決意しました。 「完全自動化」—— 人の手を一切介さない“バリ取り自動化”の実現。 本記事では、バリ取り自動化の歴史を振り返りながら、当社開発の「バリ取り完全自動化」技術について詳しく解説していきます。 過去導入していたが、精度がイマイチで辞めてしまった… 導入したいが、FA化の担当者がいなくて見送っている… という方に向けて、当社の想いと開発背景を記していますので、ぜひ最後までご覧ください。 そもそもなぜ“完全自動化”は実現できなかったのか? 近年、熟練工が培った技術やノウハウの伝承が追い付かず、「熟練工が徐々に退職し始めている…」、「後継者が思うように育たない…」という課題解決に向けて、ロボットでバリ取りを自動化するといったニーズが高まっています。 一方でロボットは、ティーチング(教示)された動作しかできないため、イレギュラーな形状のバリに対して臨機応変にバリ取りすることができません。 そのためロボット導入がさかんになってきているものの「ある程度ロボットで素早く削って、残りは作業者が仕上げる」という、謂わば“半自動化”が製造業界の当たり前となってしまい、熟練工の技をロボットで再現するのはそもそも不可能と認識されてきたことが、完全自動化が実現していない大きな要因です。 このバリ取りロボットの“精度の低さ”により、冒頭でもお話した「過去導入していたが、精度がイマイチで諦めてしまった…」という企業様が多くいらっしゃるのが現状です。 FINESYSTEMは、この日本のモノづくりに対する「諦め」をなくすべく、バリ取りの“完全自動化”に向けて、研究・開発を始めました。 “完全自動化”の実現に向け、 熟練工の技を再現する「ホルダ構造」に着目 バリ取りを完全自動化するためには熟練工の技、つまり「手首の動き」を再現する必要があります。先の通り、ロボット最大の欠点は、ティーチングだけではイレギュラーなバリに対応できないこと。 ここで当社が目をつけたのが、熟練工の技を再現する独自の「ホルダ構造(機構)」の開発です。 従来ホルダの構造とデメリット まずはバリ取りロボットにおけるホルダとは何か?を紹介していくとともに、従来のバリ取りホルダにどんな問題点があったのかを解説していきます。 リジッド機構:「空振り」が発生してしまう ▲リジッド機構イメージ 初期のバリ取りロボットは、工具を軸先に固定する「リジッド機構」が主流でした。 リジッド機構は工具のブレが少ない反面、バリの形状・大きさに合わせた柔軟な動きができず、空振り(削り残し)が発生していました。 そのため「ロボットを導入したけど、手作業の方が精度が高い…」「結局残ったバリは、手作業での仕上げが必要…」といったケースが多くあり、ロボットで作業すべてを自動化する、というのが難しいホルダ機構といえます。 バネ機構:「えぐり」の発生が問題に… ▲バネ機構イメージ その後、より”人の手に近い動き”を再現するために「スプリング(バネ)の力」を応用したホルダが開発されました。バネ機構はバネの伸縮により工具をワークに倣わせることで、ある程度ティーチングから外れた動きが可能となり、人の手のような柔軟性を実現しました。 一方で傾動・伸縮はするものの、フロート(圧力)の発生源はバネですので、作業の途中でフロート力(バネ自体の圧力)の調整が必要な場合には、作業を中断して「バネ自体の交換作業」が発生するといったデメリットがありました。 またバネによるフロート力は、押し付けるほど反発して強くなるため、反発が強すぎて製品までえぐってしまう事例も目立つようになっていました。 これらの「空振り・えぐり」は必ず出てしまうもの。であれば、ここの仕上げは作業者に任せよう、という考え方が当たり前になり、バリ取り自動化は名ばかりの「半自動化」という業界認識が広まってしまったのです。 FINESYSTEMの答えは、 空振り・えぐりゼロの「熟練工レベルのバリ取り加工技術」の開発 そもそも熟練工がロボットに勝る理由は、“己の感覚”を作業に落としこめること。当社はバリ取りロボット最大の課題である「空振り・えぐり」をゼロにするためには、ロボットにも”感覚作業に近い動き”をさせることが重要と定義づけました。 そこで設計・開発したのが、FINESYSTEM特許技術である「独自のエアフロート機構」です。 独自エアフロート機構搭載、『AFシリーズ』の特徴 独自エアフロート機構は、フロート力に圧縮エアを用いる機構をベース構造としつつ、軸元に「複数ボールガイド(特許技術)」を使用することで、刃先がワーク形状に素早く滑らかに追従し、機械でありながらより“感覚作業”に近いバリ取りを実現しました。 これまでバリ取りロボットは、ワーク形状にあわせて綿密なティーチングを行う必要がありましたが、独自エアフロート機構では動画のように「ここから、ここまで削る。」という最低限のティーチングを行うだけで、まるで熟練工の手首のように、工具をワーク形状に倣わせることが可能に。 これにより、従来機よりもティーチング点数を減らしサイクルタイムが向上するだけでなく、バリ取りロボット最大の課題だった「空振り・えぐり」ゼロを実現したのです。 その他の作業も「完全自動化」を実現! バリ取り作業はもちろん、ロボットを利用する上で欠かせない、 フロート圧の変更 工具(ツール)交換 これらの作業も、電空レギュレータやATC(工具自動交換システム)を用いることですべて自動化。これにより“ロボットそのものの操作”さえも人の手を一切介入させない、本当の意味での「バリ取り完全自動化」を実現させました。 当社バリ取りロボットの特徴をより詳しく知りたい方は、下記ページもご覧ください。 関連ページ:『バリ取り自動化』 金属だけでなく、樹脂も対応可能! まずは「事前トライ」で課題感をお聞かせください 本記事でも紹介した通り、当社は「以前導入していたけれど、諦めてしまった…」という企業様の悩みを踏まえて、今日まで研究・開発を行ってきました。 そのため、 進化したロボットは気になるけど、また同じ結果にならないか心配… 自社製品のバリ取りを自動化できるのか… といった不安を解消すべく、実際の「お客様の製品・ワーク」を利用した「事前トライ」を承っております。 実際に加工した際の品質はどうか? サイクルタイムをどのぐらい削減できるのか? 導入時の「費用対効果」はどうか? なども踏まえて解決策をご提案いたしますので、まずはお気軽に事前トライにてご相談くださいませ。 >バリ取りトライのお申し込みはこちらから!