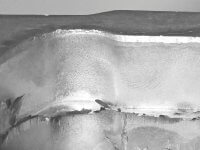
2023.11.30
金属バリ取りはなぜ難しい?理由や実際の「バリ取り方法」を解説
そもそも「バリ取り」って何? バリとは、金属加工や樹脂(プラスチック)加工の過程で発生する、突出部や余分な部分を指し、一般的には不規則で鋭角な形をしています。また金属の鋳造や樹脂の射出成形のような「型」を利用した加工においても、バリは発生します。 このときのバリの発生原理としては、鋳造や成形中に型の合わせ目や部品と型の間隙から材料が漏れ出し、その部分が固まり、型などの合わせ目に沿った形状のバリとして現れるのです。 <金属の切削加工バリとアルミダイキャストの成形バリの例> 切削や成形の他にも溶接や表面処理などさまざまな場面でバリは発生しますが、部品の精度向上・利用者へのケガ防止などのためにも、必ず取り除くべき存在とされているのです。 発生したバリを除去する工程を「バリ取り」といいます。 下記記事では「バリ取り」についてより詳しく解説していますので、ぜひこちらもあわせてご覧ください。 関連記事:『バリ取りって何?「バリ」の発生原因から行う理由・方法まで詳しく解説!』 金属のバリ取りが難しい「5つ」の理由 ①:他素材と比べて「硬さ・強度」が高いから 金属の「硬さ」「強度」は、金属バリ取りを難しくさせる大きな要因です。 特に、硬度が高い鋼やチタンなどを含む合金の場合、一般的なヤスリなどの工具では簡単には削除できない固いバリが形成されることがあります。 また、金属の硬度によっては、工具の摩耗が激しくなり、頻繁な交換が必要になることもあるのです。 ②:「バリの種類」がさまざまだから 金属製品は加工方法によってそれぞれ異なる種類のバリを生じます。 例えば鋳造であれば、金属が型に流し込まれる際、型の細かい隙間から微細なバリが生じ、これらのバリは非常に小さく、取り除くのに工夫が必要です。 また切削では、刃物や砥石が素材を削り取る際にバリが生じることがあり、形状が複雑なバリが発生しやすいです。 このように金属製品の「加工方法・製造過程の違い」によって、さまざまな形状のバリに対応していかなければいけないのです。 ③:「精度・品質」の要求値が高いから 金属製品はその強度から、自動車部品や医療器具などの精密機器の製作にもよく利用されます。 当然これらは「精密機器」なわけですから、バリの削り残しはあってはならず、確実にバリを取り除かなければいけません。 もちろん、バリの削り残しは「製品の安全性」にも直接関係するため、上記のような精密機器の場合では、微細なバリひとつが人間に被害をもたらす場合すらあるのです。 そのため、バリ取り作業も非常に慎重に行う必要があり、作業者の経験や熟練の技術が不可欠となってくるのです。 ④:バリ取り技術に限界があるから バリ取りにもさまざまな方法がありますが、もちろんそれぞれ、バリ取りできる範囲には限界があります。 手作業によるバリ取りであれば、機械では難しい作業ができますが、非常に労力がかかり、精度も「作業者の技術」に大きく依存する上、大量生産には向いていません。 機械によるバリ取りであれば、製品形状の変化などに対して柔軟な対応が難しく、細かいバリや複雑な形状のバリの除去が困難です。 このように目的や製品に応じた適切なバリ取り方法を選択することが、金属バリ取りを難しくしている要因でもあるのです。 そのため近年では、バリ取り機を「ロボット」に置き換え、バリ取りの自動化を行っている企業も増えつつあります。 ⑤:バリ取り自体が「危険な作業」なため 手作業によるバリ取りでは、切削工具(ベルトサンダー、ハンドリューター、ヤスリ)などが使用されますが、バリや工具で手を切るなど、作業者が怪我のリスクを伴います。 研磨材を使用したバリ取りでは、微細な粉塵が発生することがあり、これが呼吸器系の健康問題を引き起こす可能性もあるわけです。 そのため「効率と安全のバランス」を取りながら、バリ取り品質を確保することが、バリ取り工程における大きな課題となっているのです。 下記記事では、金属とあわせてバリが発生しやすい「樹脂(プラスチック)バリ」の特徴について詳しくまとめていますので、金属バリについてお悩みの方は、下記記事もあわせてご覧ください。 関連記事:『樹脂(プラスチック)バリ取りはなぜ難しい?樹脂向けの「バリ取り方法」を解説』 金属のバリ取り方法とは? 金属製品のバリは、樹脂などのバリと比べて硬いため、より丁寧にバリ取りする必要があります。 ここからは金属製品のバリ取り方法について、詳しく解説していきます。 手作業によるバリ取り 手作業工具(やすりやスクレーパー、研磨ベルトなど)を使った、最も一般的なバリ取り方法です。 人の手で直接除去するため、確実にバリを取り除ける反面、人件費や出来栄えが「作業者の腕」次第で変わってきてしまうのがデメリットといえるでしょう。 機械によるバリ取り マシニングセンタや複合旋盤などの機械に、カッターやブラシなどを取り付けてバリ取りする方法です。機械によるバリ取りでは、品質にバラツキがなく効率的にバリを除去でき、全体の加工時間を短縮できるメリットがあります。 一方で、一台で「すべてのバリ取り」ができるとは限りませんので、いろいろな種類のバリ取り機を導入しなければならない、といったデメリットもあります。 ロボットによる自動バリ取り 近年では、ロボット技術を利用した「バリ取りの自動化」を行うケースも多くなってきました。 これまでロボットを使ったバリ取りというと、大掛かりな機械の導入が必要なことが一般的でしたが、小型ロボットを使用すれば、大掛かりな設備準備の必要もなく、経済的にバリ取りを自動化できるようになりました。 またこれまでのバリ取り機では、製品形状に追従しないため熟練工の手作業によるバリ取りと同等の品質を提供することが難しいという課題がありましたが、近年では技術進歩により、ロボットによるバリ取りでも、「熟練工の技」に匹敵する品質を実現できるようになってきたのです。 関連記事:『バリ取りロボットで作業を自動化!導入費用やメリットまで詳しく解説!』 参考記事:『金属加工の「バリ」とは?発生原因やバリ取りの方法、抑制のコツを解説|さくさく株式会社』 FINESYSTEMの「バリ取り自動化」技術で 金属製品のバリ取りに大きく貢献! 本記事でも解説した通り、金属製品のバリ取りは、ミリ単位の削り残しや、金属独自の「硬度」にも対応すべく、基本的には手作業で行われるのが一般的でした。 しかし近年では、バリ取り工具やバリ取りロボット技術の進歩により、金属のような硬い材質であっても、ロボットによるバリ取りの自動化が行えるようになりました。 また、バリ取り自動化を前向きに検討されている企業の中でも、 自社でできるかわからない… 導入後のプログラミング(ティーチング)ができる技術者がいない… ロボットに熟練工レベルの仕上がりが再現できるのか不安… などのお悩みから、導入を諦めてしまう企業様も少なくありません。 FINESYSTEMでは、ロボットを活用したバリ取りに関するあらゆる自動化で、お客様のお悩みを解決し生産性向上のお手伝いをします!「無償バリ取りトライ」も行っており、事前にバリ取り品質をご確認いただけます。 バリ取り自動化を検討しているが、どこに依頼すべきか分からない 自社製品に見合ったクォリティが出せるか、確認してから依頼したい 導入から保守まで全部お任せしたい 上記のような内容でお悩みなら、ぜひ一度お問合せくださいませ! >>お問い合わせはこちらから >>バリ取り・RBハンドリングのトライのご相談はこちらから 下記記事では、FINESYSTEMの自動バリ取りの品質が高い秘密「フローティング機構」について詳しく解説していますので、バリ取りロボットの導入をご検討中の方は、ぜひこちらもあわせてご覧ください! 関連記事:『フローティング機構とは|バリ取り自動化に向けて知っておきたいこと』