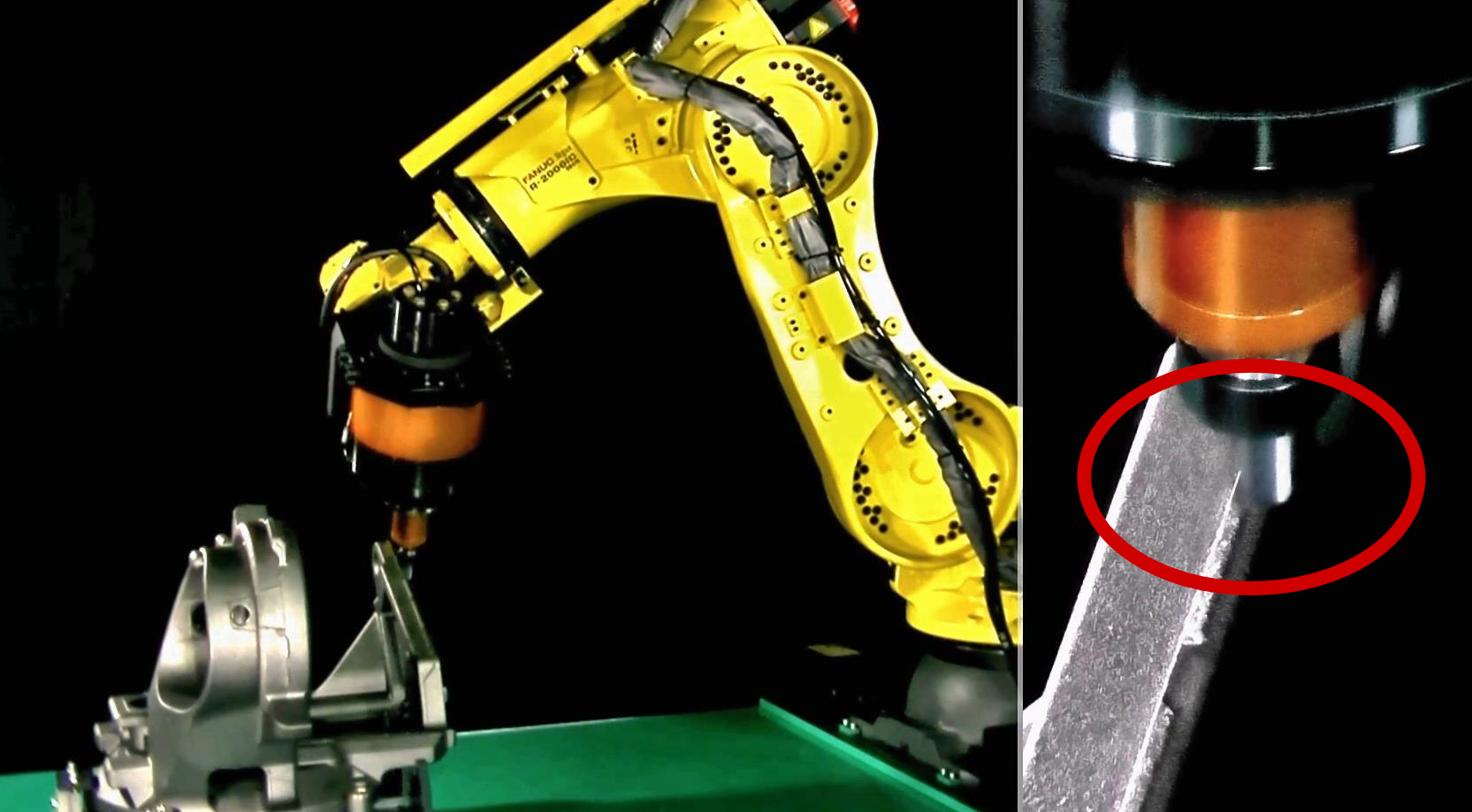
2025.05.26
ダイキャストのバリ取りも自動化!?鋳造製品の「粗加工」に必要なツールを解説
製造における「荒加工」とは 荒加工とは、大きいバリをざっくりと取り除き、ワーク形状を整える作業です。 本記事では、バリ取り自動化における第2フェーズ「荒加工」で使用する切削ツールについて詳しく解説していきます。 荒加工には“エンドミル”が主流 荒加工ツールは、切断したワークをある程度整える、いわば切断と仕上げの“中間”を担うツールです。 エンドミルは、湯口切断後のゲート跡の荒削りとして使用します。 基本的にはツールの“側面”で切削するため、広い面でざっくりとバリ取りするのに向いています。対象ワークは金属全般、主にアルミ製品(アルミダイキャスト)、鋳鉄・鋳鋼、ステンレスなど幅広く使用可能です。 特に精密な加工が必要とされるダイキャスト製品の加工については、こちらの記事で詳しく解説していますのであわせてご覧ください。 関連記事:『ダイキャスト(ダイカスト)とは|鋳造との違いや製品事例も解説』 「荒加工の自動化」の注意点 ツールは消耗品 まずエンドミルなどの荒加工ツールは「消耗品」です。そのため定期的な交換が必要となります。 また消耗具合もワークの特徴や運用方式によっても異なりますので、交換頻度は運用してみないことには分かりません。 トルク不足による「削り残し」 荒加工で大きなバリを削り取る場合、その分トルクと剛性が必要になります。 いかに切削精度の高いツールを選んだとしても、ホルダから伝わるトルクが弱いと写真のように削り残しが発生してしまいます。 当社製品(AFシリーズ)でいうと、荒加工の場合は「AF40以上」のトルク出力を推奨しています。 当社のホルダラインナップについてはこちらをご覧ください。 関連ページ:『バリ取り自動化について|株式会社FINE SYSTEM』 FINESYSTEMはラインナップを充実!あらゆるバリに対応可能! 本記事でも紹介したように、荒加工はワークによってバリサイズが大きく違うため、ツールを豊富に揃えるだけではバリ取り精度は上がりません。必要なのはワークに合うツールの準備と、それにあわせた「ホルダの選定」です。 FINESYSTEMのバリ取りホルダ「AFシリーズ」は、豊富なホルダラインナップを展開しているため、荒加工はもちろん、鋳造直後の湯口切断から、これまで熟練工の業といわれてきたきめ細かな仕上げバリ取りまでを“ロボットで自動化”できるようになりました。 当社AFシリーズのホルダラインナップ AF150 AF110 AF40 AF30 AF20 AF10 切断 〇 〇 △ × × × 荒加工 〇 〇 〇 × × × 仕上げ 〇 〇 〇 〇 〇 〇 もちろん導入サポートから、その後のティーチング、万一のトラブル対応まですべてサポート。導入前の「バリ取りトライ」も行っていますので、事前にバリ取り品質をご確認いただけます。 バリ取り自動化を検討しているが、どこに依頼すべきか分からない 自社製品に見合ったクォリティが出せるか、確認してから依頼したい 導入から保守まで全部お任せしたい 上記のような内容でお悩みなら、ぜひ一度お問合せくださいませ! >バリ取りトライのお申し込みはこちらから!