そもそも「バリ取り」って何?
バリとは、金属加工や樹脂(プラスチック)加工の過程で発生する、突出部や余分な部分を指し、一般的には不規則で鋭角な形をしています。また金属の鋳造や樹脂の射出成形のような「型」を利用した加工においても、バリは発生します。このときのバリの発生原理としては、鋳造や成形中に型の合わせ目や部品と型の間隙から材料が漏れ出し、その部分が固まり、型などの合わせ目に沿った形状のバリとして現れるのです。
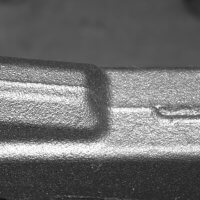
<金属の切削加工バリと鋳造バリの例>
切削や成形の他にも溶接や表面処理などさまざまな場面でバリは発生しますが、部品の精度向上・利用者へのケガ防止などのためにも、必ず取り除くべき存在とされているのです。
発生したバリを除去する工程を「バリ取り」といいます。
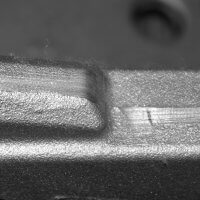
<バリ取り後の例>
下記記事では「なぜバリが発生するのか?」について、より詳しく解説していますので、こちらもあわせてご覧ください。
関連記事:『バリ取りって何?「バリ」の発生原因から行う理由・方法まで詳しく解説!』
手作業のバリ取り精度を高める「6つ」のコツ
ひとえにバリ取りといっても、正確さが求められます。特に手作業でのバリ取りにおいては、機械では作業が難しい部分を人の手で作業するわけですから、バリ取りの知識はもちろん、バリ取り作業のコツを掴むことも非常に重要です。
ここからは、手作業でバリ取りを行う際のコツについて6つ解説していきます!
バリに合わせた、適切な工具を選択する
適切な工具の選択は、バリ取りの品質と効率に大きく影響します。例えば金属部品のバリ取りにおいて「ヤスリ」は必須アイテムですが、そのヤスリの中にも「平ヤスリ」や「丸ヤスリ」、「三角ヤスリ」など、部品の形状やバリの位置によって適したものを選ぶ必要があります。また金属の硬さに応じて、粗い目のものから細かい目のものまで、ヤスリの目の粗さも選択するポイントとなります。
樹脂(プラスチック)やゴムの場合は、カッターナイフや専用のバリ取り工具がよく使われます。部品の複雑さやバリの大きさによって、刃の形状や大きさを選ぶことが大切です。また、バリ取り工具には回転式のものもあり、複雑な形状の部品に対してもスムーズにバリ取りができます。
上記のような「素材・形状に合わせた選択」だけでなく、自分の手に馴染む工具であることもバリ取り品質を高めるにあたって重要といえるでしょう。長時間の作業を考慮した、握りやすさや重量なども工具選択を行う上で重要視してください。
過度に力をかけすぎない
バリ取りにおける「力の加減」というのは、仕上がりの品質や部品へのダメージの有無に直結します。特に手作業の場合、感覚を頼りに力を調整する必要があるため、馴れも必要ですが、バリ取りの際に気を付けるべき「力のかけ方」を押さえておけば、ある程度の仕上がりを担保することが可能です。
例えばヤスリを使用したバリ取りの場合、はじめは軽く数回こすってみて部品の削れ具合を確認しましょう。過度に力をかけてしまうと、部品に傷がついてしまったり、必要以上に削り過ぎてしまったりといったケースもあります。
この力の確認は、ヤスリの「粗さ調整」にも影響するため、はじめから粗い目のヤスリを使用する場合は、特にこの力の確認を行うようにしましょう。カッターナイフやバリ取り工具を使用する場合、刃先が鋭利であるため、過度に力をかけかけないようにしましょう。これも上記同様に、部品を傷つけたり、必要以上に削り過ぎてしまったりするリスクがあります。そのため、バリ取り工具をバリに軽く当てて、滑らせるようにバリを取り除くのが基本です。
「適切な角度・持ち方」を意識する
バリ取りを行う際、工具を部品に対して適切な角度で当てることも、部品へのダメージを最小限に抑えるために意識すべきポイントです。平面のバリ取りでは、ヤスリを部品に対して約45度の角度で当てるのが一般的ですが、曲面や狭い場所のバリ取りでは、作業者の感覚で角度を調整する必要があり、この角度については、馴れが必要となるでしょう。
工具を当てる角度だけではなく、作業時における「手の位置・持ち方」も角度の安定性に影響します。工具をしっかりと握り、部品に対して安定した角度を保ち続けることで、均一な仕上がりを得ることが可能になります。繰り返しの作業で疲れてくると、手の動きが乱れやすくなりますので、一定の角度を保てるようなブレのない姿勢での作業が好ましいです。
光の角度を変えて確認する
バリ取りを行っている最中も、適宜、光の当て方を調整しながら、「バリの取り残しがないか?」などを確認しながら作業を進めましょう。特に微細なバリなどは、直接的な光のもとでは見逃しやすく、削り残しの原因となります。そのため、作業ライトや手元の光を異なる角度から当てて、反射や影の変化を確認することで、見落としていたバリ発見するようにしましょう。
また、持ち手の位置を変えて部品を光に対して動かすことで、部品の表面の状態をさまざまな角度から観察することができます。このようにして、常に最適な視点と光の角度を確保しながら作業を進めることで、バリ取りの品質を一段と高めることができます。特に複雑な形状の部品や細部のバリ取りが必要な部品の場合、この方法は非常に効果的です。
このように、光の角度や部品の持ち方を適宜調整しながら作業を行うことで、より品質の高いバリ取りが可能になるのです。
定期的にバリ取り状態を確認する
バリ取りは細やかな作業であるため、一度で完璧に取り除くことは難しいものです。そのため、「一定範囲を削った」「ある程度の時間作業を続けた」などキリの良いタイミングで進行状況を確認することが大切です。また確認の際には、手で部品を触って確認するのはもちろん、目視で細かい部分まで丁寧にチェックを行いましょう。
作業後のクリーニングまで丁寧に
一通りバリ取りが完了しても、部品には細かなバリの破片や工具からの微細な粉末などが残存しています。これらのバリの破片が残ったままになっていると、組付けなどの次の工程において、組付精度の悪化などの問題を引き起こす可能性があるため、念入りなクリーニングが必要です。
またクリーニングを行うことで、削った後の粉末かと思っていたものが「小さなバリ残りだった」と気付くケースも少なくはありません。そのため最後のクリーニングも怠らずに、しっかりと仕上げを行うようにしてください。
おすすめの手作業用バリ取り工具は?
ベルトサンダー
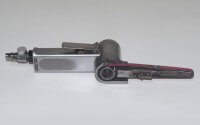
ベルトサンダーとは、電気または圧縮エアで動作するベルト状の研削工具です。その高い効率性と研削力は、大量のバリ取りを短時間で仕上げる必要がある場合に特に役立ちます。一方で、ベルトサンダーの操作には慣れが必要であり、動力と作業スペースも確保する必要があるため、使用場所が限られてしまうことを念頭においておく必要があります。
ハンドリューター
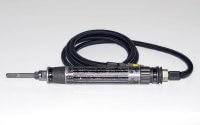
ハンドリューターはバリ取りにおける精密作業箇所で使用される回転工具で、特に手作業では届きにくい狭いスペースのバリ取りに適しています。またハンドリューターは回転速度調整が可能で、多種多様なビット(刃先)を取り付けられることからも、バリ取り作業に応じたカスタマイズが可能なことも、大きな特徴です。
ヤスリ
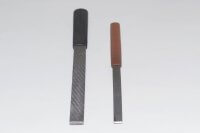
ヤスリは多くのバリ取り作業に使われる基本的な手作業工具です。手作業バリ取りにおけるヤスリの特長は、道具の形状も扱いやすさもシンプルで、直感的にバリ取りができることにあります。特に精密な作業が必要な場合や、電源がない環境での作業には非常に適しており、最終的なバリ取り仕上げによく用いられます。しかし、細かな作業が可能な反面「効率性」という面では他の道具に劣るため、あくまでも「仕上げ加工」として利用するのがベストでしょう。
近年はロボットによる「バリ取り自動化」も
手作業でバリ取りを行うことも綺麗に仕上げるために重要ですが、近年ではバリ取り機やロボットを使用し「バリ取りの自動化」を行う企業も多くなってきています。
ロボットによるバリ取り作業は、作業者の負担を軽減でき、何より「作業者不足」といった状況を解消します。手作業でのバリ取りを担当する熟練工が高齢化する中、バリ取り業界では人手が不足しており、作業者にとっての負担も大きくなりつつあります。そこでロボットの導入により、これらの問題が解消されるのです。さらに、ロボットは高速で作業を行えるため、生産性と作業効率が向上します。人が行う作業では定期的な休憩が必要ですが、ロボットにはその必要がないため、作業効率が一層高まります。
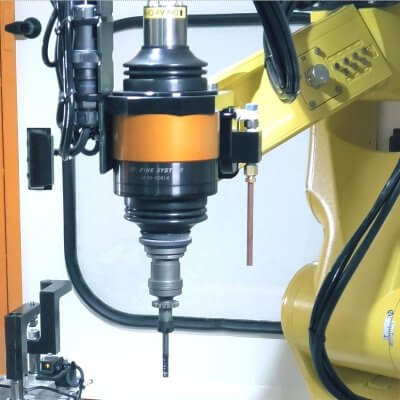
また「繰り返し作業」「作業精度」においてもロボットは優れており、ロボットにエアフロート式バリ取りアタッチメントを搭載することにより、倣い加工が可能となりバリを確実に除去することができます。
「バリ取り自動化」をご検討中の方は、下記記事で詳しい導入費用・メリットについて解説していますので、こちらもあわせてご覧ください。
関連記事:『バリ取りロボットで作業を自動化!導入費用やメリットまで詳しく解説!』
エアフロートアタッチメント対応のベルトサンダーユニットで
バリ取りをさらに自動化!
前述した手作業用バリ取り工具「ベルトサンダー」も、FINESYSTEMではロボットで自動化。
当社が提供するベルトサンダーユニットは、当社製品エアフロートアタッチメントAF40型に装着することで、これまで手作業に頼っていたベルトサンダー加工をロボットで自動化!
エアフロートの「倣い機構」とベルトサンダーの「研削力」を組み合わせることで、安定したバリ取り品質を実現。
また、ワークの形状に応じて自動的に工具が倣うため、複雑形状のバリ取りにも柔軟に対応可能です。
FINESYSTEMの「バリ取り自動化」技術で
バリ取り業務の大幅改善に貢献
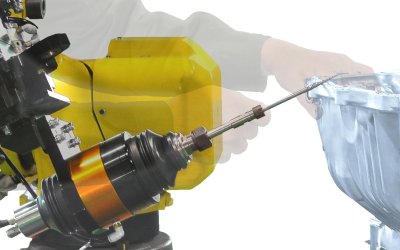
FINESYSTEMでは、これまでバリ取り工程において課題視されてきた、高い品質や工数、作業者不足などの課題を解決するため、「熟練工レベルのバリ取り」を実現するバリ取り自動化システムおよび、バリ取りホルダやツールの開発・製作を行って参りました。
- バリ取り自動化を検討しているが、どこに依頼すべきか分からない
- バリ取り品質は維持しつつ、「生産性向上・コスト削減」を行いたい
- 作業者の負担を減らしたい
上記のような、バリ取り自動化による作業改善なら、ぜひFINESYSTEMにお任せください!
>>お問い合わせはこちらから
>>バリ取り・RBハンドリングのトライのご相談はこちらから
下記記事では「熟練工レベルのバリ取り」を叶える、当社の『エアフロート機構』について詳しく解説していますので、ぜひこちらもあわせてご覧ください!
関連記事:『フローティング機構とは|バリ取り自動化に向けて知っておきたいこと』