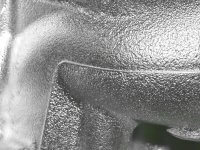
2023.11.24
ダイキャスト(ダイカスト)とは|鋳造との違いや製品事例も解説
ダイキャスト(ダイカスト)とは? ダイキャスト(ダイカスト)とは、アルミニウムや亜鉛、マグネシウムなどの非鉄金属の合金を高温で溶かした状態で、高速・高圧で金型に流し込んで成形する「鋳造法」のひとつです。圧力をかけて成形することから、金型によっては、複雑で精密な形状の成形できることが大きなメリットとされています。 またダイキャストは、砂型鋳造や重力鋳造、金型鋳造などの他の鋳造方法とは異なり、高い寸法精度や優れた鋳肌面、そして設計の自由度も大きな特徴です。 これにより近年では、自動車部品をはじめ、オフィス機器や電化製品など、さまざまな精密機械の製造に利用されているのです。 さらに大量生産にも対応しやすく、コスト面での利点も見逃せません。中でも、アルミニウムはその軽さと、耐久性、リサイクル性、そして省エネルギー性に優れ、ダイキャスト材料として特に重宝されています。 ダイキャストと「その他の鋳造」との違いは? 先にダイキャストは鋳造法の一種と解説しましたが、具体的には鋳造とどのような違いがあるのでしょうか? ダイキャストと鋳造はどちらも溶かしたアルミ合金などを金型に流し込んで成形する製造方法で、金型に流し込む「圧力・充填スピード」以外には大きな違いはありません。 この圧力と充填スピードの違いにより、複雑で精度が必要な製品でも金型に流し込むという一つの工程で製造でき、生産性が高く、大量にしかも低コストの製品づくりが可能となります。 ダイキャスト(ダイカスト)のメリットは? 寸法精度が良く複雑な形状の製品にも対応できる ダイキャストはアルミ合金などを溶かして高速・高圧で金型に流し込んで成形するため、複雑な形状であっても、精密かつ効率良く製造することが可能です。鋳物は精度を出すのが難しいとされますが、ダイキャストの大きなメリットとして、高い寸法精度を出せるという点が挙げられます。 例えば、自動車やオフィス機器、電化製品の部品など、「精度」が求められる細かい部分でも、ダイキャストにより高い品質での大量生産ができるというわけです。 加工表面が滑らかに仕上がる ダイキャストの特徴は複雑な形状に対応できるだけではありません。 鋳物には鋳造特有の鋳肌が出てしまうものですが、ダイキャストは表面が滑らかに寸法精度良く仕上がるため、砂型鋳造や重力鋳造、金型鋳造などの他の鋳造方法よりも優れた方法として知られているのです。 <ダイキャストと砂型鋳造との鋳肌の違い> コスト削減が可能 ダイキャストは、複雑で精度が必要な製品でも金型に流し込むという一つの工程で製造できるため生産性が高く、寸法精度が良く表面も滑らかに仕上がり大量生産向きの製法といえます。 例えば先に述べた自動車やオフィス機器、電化製品の部品などは、これまでは多数の精密部品を組み立てることで作られてきました。ダイキャストでは複雑な形状を高い寸法精度で成形できることから、これまで複数の部品を組み合わせていた箇所をひとつの部品として大量生産できるため、部品点数や加工・組立の工数を減らすことができ、製造コストを大きく削減できるのです。 ダイキャスト(ダイカスト)のデメリットは? 初期費用が高額で小ロット部品の生成には不向き ダイキャストは高精度で複雑な形状の金属部品を大量に作ることに適していますが、「金型自体」の製作には多くの費用がかかります。また溶かした金属を流し込む関連設備などが必要となり、ダイキャストの初期費用は高額になってしまいます。 そのため、大量生産に向けた導入でなければ、コストを回収するのが難しいのも現実です。そのため近年では、自動車部品や家電などの大量生産が必要とされ、かつ精密部品が多い分野において利用されているのです。 パイプなどのような中空形状の製品は作ることが難しい ダイキャストでは、金型へアルミ合金などを高速・高圧で流し込んで成形します。この方法では、パイプのような「内部が空洞の製品」を作るのは難しいです。 これは空洞をつくるためには、ダイキャストの型自体に閉じた空間を作る必要があるためで、金属が型のすべての隙間を埋めることが難しく、空洞部分に金属がうまく流れ込まないことがあるからです。 強度を求める製品には向かない 金型に溶けた金属を流し込む際、周囲の空気や蒸発した離型剤が製品に取り込まれてしまい、鋳巣と呼ばれる細かな穴が開いてしまうことがあります。このことから同じ材質でも、切削加工などで作られた部品に比べて強度が下がるという問題があります。 これらは製品の強度に大きく影響してしまうこともあるため、ダイキャストでは強度を必要とする製品、部品づくりには向かない傾向にあるのです。 参考記事:『ダイカスト(ダイキャスト)の特色について|大健工業株式会社』 ダイキャスト(ダイカスト)に使用される金属(合金)は? アルミダイキャスト アルミダイキャストは、その軽さと強度、熱伝導性や耐食性が特徴的で、経年による寸法の変化が少ないのが特徴です。そのためダイキャストの分野では、最も生産量が多い素材となっています。 特に近年では、車のボディパーツや内部の精密部品などに多く利用されています。 亜鉛ダイキャスト 亜鉛ダイキャストは加工しやすく、精度の高い部品を作成する際に利用されます。一方で、比重が高いため軽量化が必要な製品には適していませんが、アルミダイキャストほど強度を要求されない場合や複雑形状または薄肉形状となる場合に多く利用されています。 また、塗装やめっきなどの表面処理が容易であることが特徴です。 マグネシウムダイキャスト マグネシウムダイキャストは、軽量で比強度が強く、振動の吸収性や耐くぼみ性に優れています。実用金属の中でも特に軽量で、近年の軽量化ニーズで生産量が増加傾向にあります。 強度はアルミニウムや亜鉛に劣り、耐食性も低いというデメリットがありますが、加工性の良さ、振動吸収性の良さなどのメリットも持っているため、軽さと丈夫さを求める機械部品への採用が進んでいます。 参考記事:『ダイカストの種類と特徴をご紹介 | 帝産大鐘ダイカスト工業』 主なダイキャスト(ダイカスト)製品は? 自動車部品(エンジン、トランスミッション、ボディパーツなど) 金属製玩具(ミニカーなど) 家電部品(冷蔵庫、洗濯機、掃除機など) 事務用品(パソコン、プリンタなど) 日用品(カメラ機器、ファスナーなど) ダイキャスト(ダイカスト)製品にも「バリ」は発生する! 鋳造法同様、ダイキャスト製品にも当然バリは発生します。 金属部品のバリは、製品組み付け時のトラブルやバリの脱落・剥離によるトラブルにもつながるため、必ず処理しなければいけません。しかしダイキャスト製品は、複雑な形状にも対応できる反面、その分発生したバリを取り除く作業も難しくなってしまいがちです。 そこで近年では、ロボットを使った「バリ取り自動化」技術により、発生したバリを高い精度で取り除く方法が主流となってきています。これにより、ダイキャストによる生産性の向上と、その後のバリ取り自動化による工数削減の双方で生産性を大きく向上させる企業が多くなってきたというわけです。 下記記事では、ダイキャスト製品のバリについて詳しく解説していますので、こちらもあわせてご覧ください。 関連記事:『ダイキャスト(ダイカスト)製品にバリは発生する?バリ取り方法も詳しく解説!』 FINESYSTEMなら、ダイキャスト製品の 「バリ取り自動化」も一括サポート! 実際にダイキャスト製法を取り入れている企業の中でも バリ取りまでは効率化できていない… 自動化させても、プログラミング(ティーチング)ができる技術者がいない… ロボットに熟練工レベルの仕上がりが再現できるのか不安… などのお悩みから、導入を諦めてしまう企業様も少なくありません。 FINESYSTEMでは、ロボットを活用したバリ取りに関するあらゆる自動化で、お客様のお悩みを解決し生産性向上のお手伝いをします!「無償バリ取りトライ」も行っており、事前にバリ取り品質をご確認いただけます。 バリ取り自動化を検討しているが、どこに依頼すべきか分からない 自社製品に見合ったクォリティが出せるか、確認してから依頼したい 導入から保守まで全部お任せしたい 上記のような内容でお悩みなら、ぜひ一度お問合せくださいませ! >>お問い合わせはこちらから >>バリ取り・RBハンドリングのトライのご相談はこちらから